Friendly Workplace
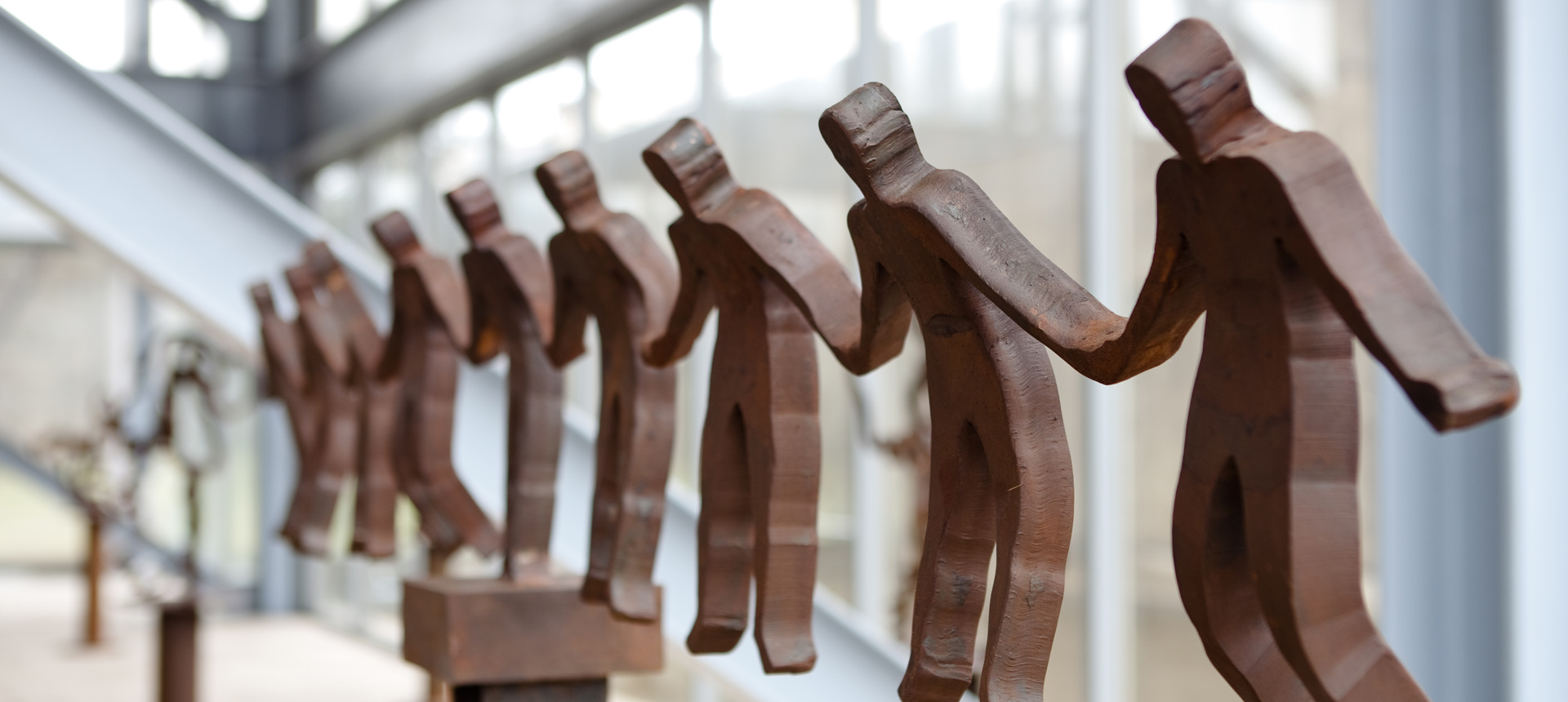
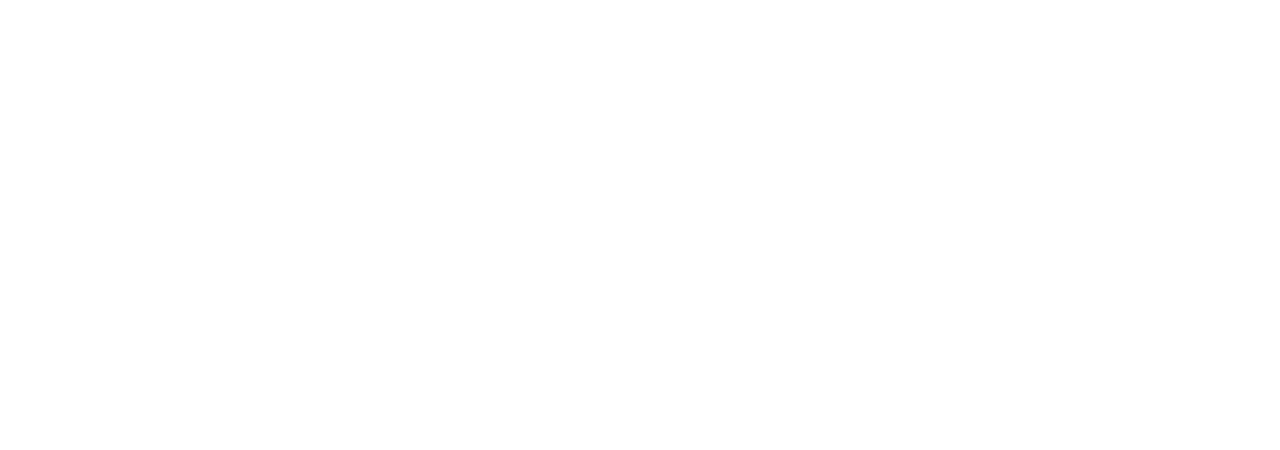
Occupational Safety and Health Committee
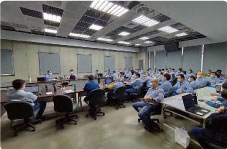
The Occupational Safety and Health Committee is composed of the head of the works, unit supervisors, occupational safety and health management personnel, occupational health nurses, and representatives assigned by the enterprise unions, with the factory director serving as the chairman and the director of the Labor Safety Center as the management representative. The Committee is convened once a month to discuss issues related to potential risks of safety and health in the works, deliberate and track safety and health meeting affairs, and make decisions and give instructions concerning safety and health related issues in the Company. The Committee is convened once a quarter in the Head Office.
The scope of the Committee’s review includes safety policies, safety and health management plans, education and training implementation plans, health management, occupational disease prevention, health promotion, occupational disaster investigation reports, contractor management, and other matters related to occupational safety and health management.
Worker representatives participating in the Occupational Safety and Health Committee are all elected by the enterprise unions, accounting for 40.6% of the committee members averagely, and our contractors/ subcontractors are also invited to participate. In terms of health and safety issues, in addition to the communication and coordination with workers for solutions in Committee meetings, education and training for new employees, monthly industrial safety inspection, safety observation, safety talks, annual health checkups, and health management. Activities such as industrial safety promotion meetings and propaganda of occupational preventions of the Labor Inspection Office are organized on an irregular basis. Health and safety related issues have been included in the collective agreement signed between Miaoli Works and the enterprise union in 2020.
Contractor Management
In the safety and health hazard risk assessment regulations, the activities and works related to our contractors/ subcontractors have been included into risk identification and assessment. In addition, safety and health operations as well as safety and health violation control and punishment regulations are included in the contract. The violation fines have dedicated usage, and are specially used to pay for safety and health rewards or for the purpose of improvement or education and training. Regular inspections and audits are carried out on the subcontractors stationed in the works. The Labor Safety Office makes annual assessment, and those who fail the assessment shall not renew the contract. Workers from the subcontractors are also required to participate in safety and health education and training courses held in the works or participate in the health lectures in the meetings of the Occupational Safety and Health Committee and the coordination of important matters in the coordination organization meetings to be informed of new knowledge of safety and health for bilateral communication.
A total of 190 subcontractors received the evaluation, and the passing rate reached 100%; a total of 152 third-party manufacturers participated in safety and health educational training.
Performance of Industrial Safety
The goal of occupational accident management in all plants aims at zero-disaster as an indicator for enhancing various safety activities in the works. Zero-disaster related activities are supported by providing incentives and commending units with outstanding results. Cause analysis is conducted for each occupational accident in the Occupational Safety and Health Committee meeting, and improvement measures are also presented. In addition to the discussion of the analysis and corrective measures of the occupational accidents in the previous month reviewed by the president, the Audit Office and the Labor Safety Centers in all factories will also conduct joint cross-plant inspection every quarter and report to the president the deficiencies and corrective measures. For major occupational accidents that require hospitalization, the section chief and the division head should conduct monthly and factory director and deputy factory director should conduct autonomous management every two months and report to the president for review. For the accident victims, in addition to necessary first-aid and rescue, the Company will also do its best to assist the employees or their family members with necessary medical care and bereavement allowances.
Reducing Risk of Occupational Accidents
The Company followed the Occupational Safety and Health Administration’s technical guidelines for all safety and hazards around the workplace caused by operating activities inside and outside the factory area (including routine and non-routine activities, workers and visitors entering the factory area, personal behavior, and other human factors), and set up the safety and health hazard identification risk assessment regulations and related procedures for risk assessment, the implementation of identification, assessment and control of the work environment and hazards.
Identification and assessment results have to be classified into different levels for control. For the unacceptable medium- and high-level of risks, actions and measures are taken to reduce the level of the risk. For the accidents that have happened, hazard identification and assessment have to be done again, the operating standards have to be revised, and the education and training of hazard awareness and identification should be implemented to conduct risk classification management and control to ensure the effectiveness of the management system. All the personnel performing hazard identification and hazard assessment are provided with education and training to ensure the quality of identification.
In 2023, hazard identification and risk assessment were carried out, and a total of 20 cases with medium and high risks were identified. Management plans were formulated for improvement and have been implemented respectively.
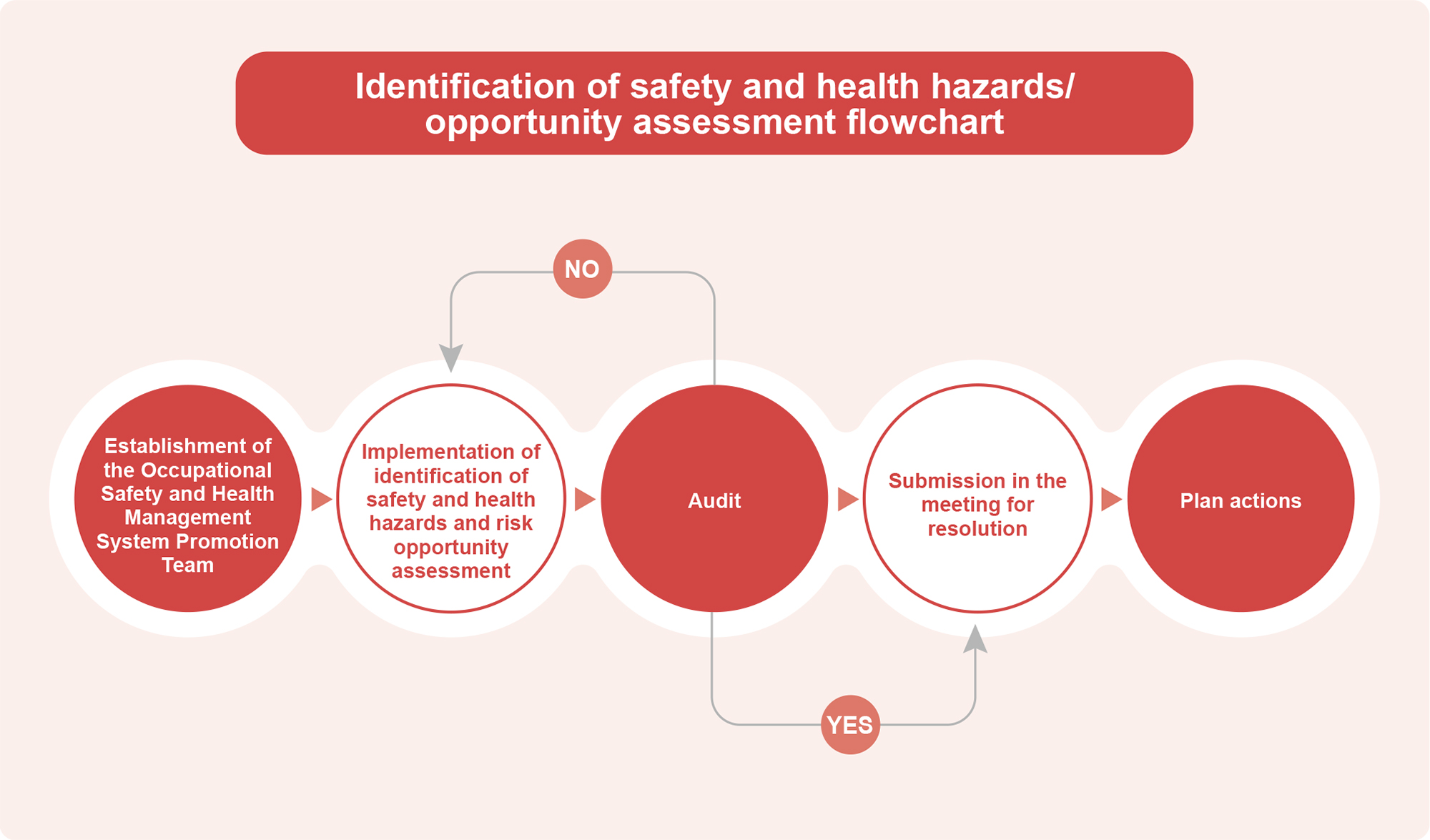
Control and Prevention of Abnormalities
In terms of the operating mechanism of accident management, electronic information management system and on-site incident drills are utilized for the statistics of occupational accidents and cause analysis, and relevant supervisors and parties jointly convene an investigation meeting to thoroughly understand the problem. The investigation results are t remedial and improvement measures to eliminate the causes of similar incidents to prevent them from happening again. all the incidents will be submitted to the Occupational Safety and Health Committee meetings for review. Respo shall reexamine the risk assessment in accordance with the safety and health hazard identification ris regulations and make revisions when necessary to establish a complete notification and investigation system.
In view of the unsafe behavior and unsafe environment that cause harm, the AI Team of the Information Technology Division applies AI image automatic detection, surround view monitoring system, and AI automatic protection de operation when detecting the entry of personnel, and warning notification or PA loudspeaker dispersion is immedia control or manage unsafe behavior or environment for improved on-site safety and health management.
In accordance with the relevant operating procedures for emergency response, when there is concern of immediate danger in the workplace, the employer and the person in charge of the workplace shall stop the operation at once and evacuate the workers to a safe place. When a worker discovers immediate danger while performing his duties, he shall stop the operation on his own and retreat to a safe place without jeopardizing the safety of other workers, and immediately reports to his direct supervisor. The Company will never dismiss, transfer, or fail to pay the wages during the period of the work suspension or impose unfavorable punishment to the work under the circumstances mentioned above.
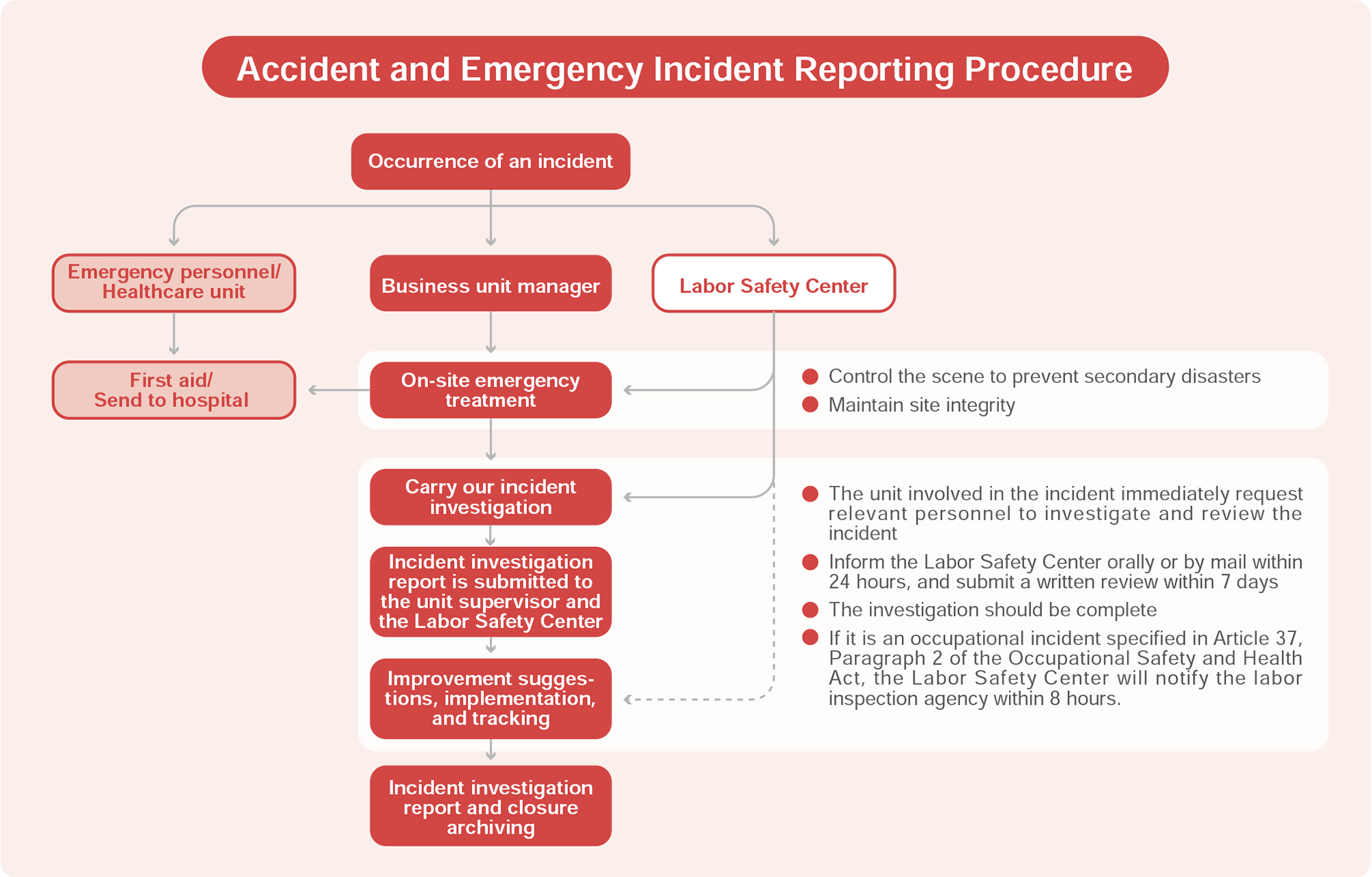
Environmental Monitoring and Disaster Prevention Drills
The Company set up work environment monitoring plans and flowchart in accordance with the “Measures for Implementing Exposure Monitoring in the Workplace”, and a quality work environment monitoring agency is appointed for the implementation of regular work environment monitoring on the Head Office and the all Worksnote, and the items include noise, comprehensive temperature heat index carbon dioxide, chemical substances (manganese compounds, sulfuric acid, butanone), illuminance monitoring, and dust. Improvement will be immediately made if there is any abnormality found in the monitoring results to protect the health of the personnel. In 2023, the monitoring results showed that the noise level slightly exceeded the standards. Subsequent monitoring will be conducted to ensure the employees use protective gear. All the other items are compliant with statutory standards.
To improve the on-site emergency response capabilities in all the works to avoid or reduce injuries of personnel, property loss and environmental impact, various emergency response drills are conducted according to the on-site operation risks. In 2023, a total of 27 sessions of emergency response and disaster prevention drills were held (17 emergency response drills, 10 firefighting drills), and the content included emergency response drills for liquefied petroleum gas (LPG) tanks, wastewater treatment equipment failures, steelmaking/rolling air pollution, emergency response drills for personnel injured by falling objects and falling into coma, emergency response drills for personnel in shock during operations, confined space operations and earthquake escape emergency response drills, self-defense fire prevention education and training, disaster prevention and escape drills, etc.
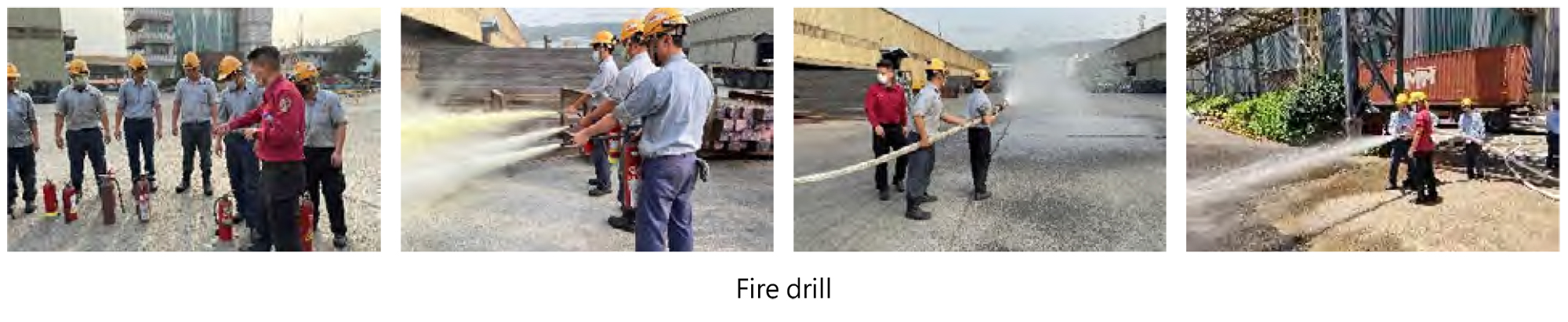
Health Examination and Care for the Employees' Health
The Company provides employee health checkups exceeding the frequency and items required by law, including general health examination and special health examination so as to provide the employees with a healthy and hygienic working environment. In addition, professional physicians will conduct statistical analysis of the health management based on the health check reports. The employees will be reminded of follow-up diagnosis and treatment of abnormal conditions, and the health promotion policy for the following year is also planned to provide comprehensive health care and assist our employees with the implementation of self-care management.
The works control the hazards of the working environment and the employees’ health through Measures for Implementing Exposure Monitoring in the Workplace and the special health examination, and the employees’ relevant knowledge of emergency treatment of burns and scalds is also promoted. If an abnormal case is found, the Labor Safety Center will conduct case management, and the physician of occupational medicine will provide one-on-one consultation to comprehensively evaluate the factors of the employees’ work nature, lifestyles, family history and others to provide suggestions for improvement for the employees and the Company. Furthermore, through hazard education and training, the wearing of protective equipment and inspection are promoted, significantly reducing the personnel’s exposure to danger and health hazards, reducing the probability of occupational diseases to the minimum. There has not been any case of occupational disease among our employees over the past 5 years, and there has been no occurrence of occupational disease among workers (whose work and workplace are under the control of the organization).
In all the works, the on-site physician will arrange health consultations for our employees, and the relevant records are kept in the Labor Health Service Implementation Record Sheet (including three non-employee workers). In addition, personnel whose health management is of level 2 or higher in the special health examination will be arranged with health lecturers and individual doctor consultations. When there are still personnel exposing to work hazard on site, hazard control and relevant management measures should be immediately conducted.
The Company establishes the health service plan based on the Occupational Safety and Health Act and Regulations of Labor Health Protection and adopts relevant regulations concerning labor health protection and safety and health measures, coupled with the provision of integrated employee health service by professional physicians.
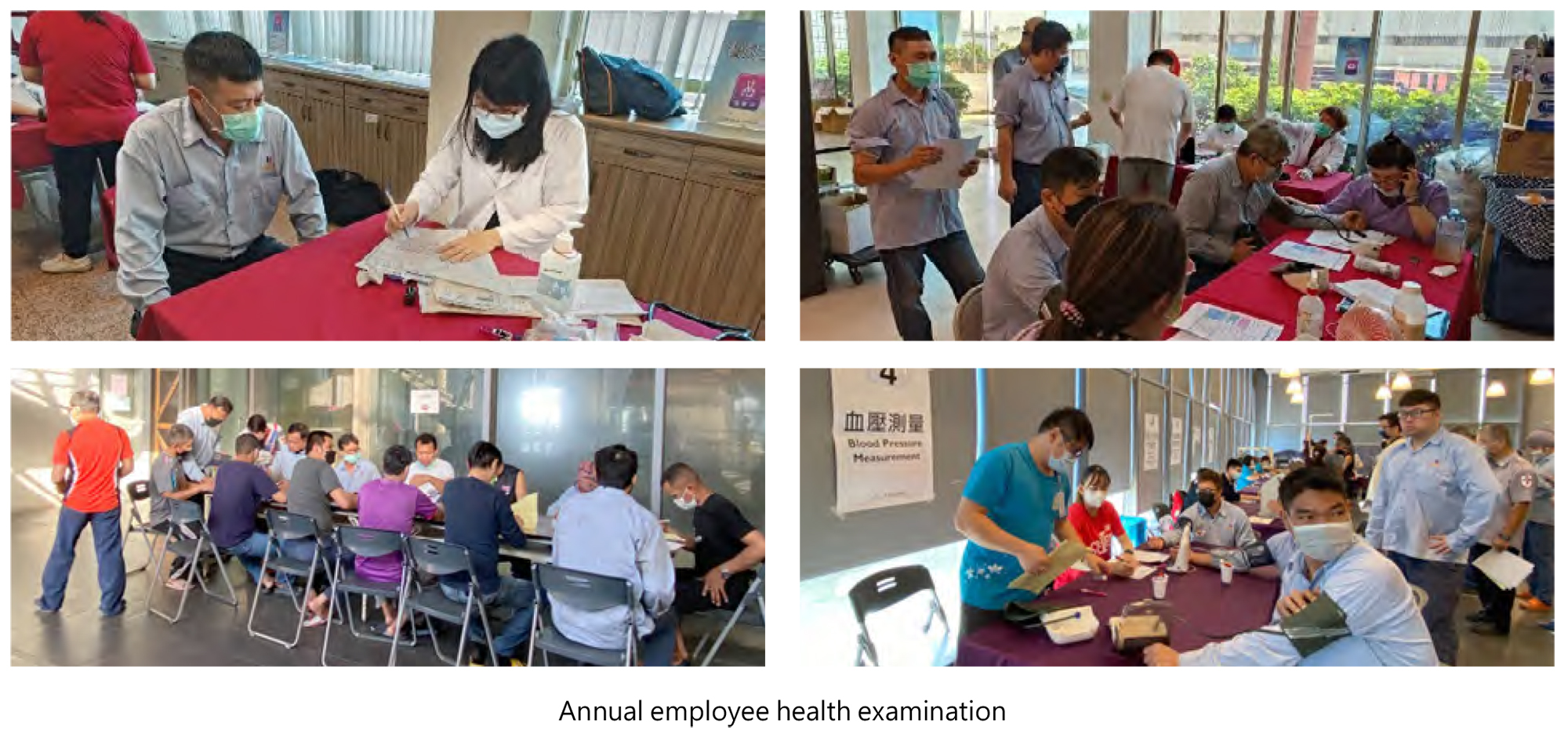